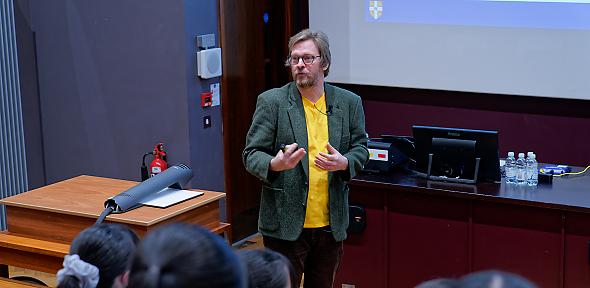
Erwin Reisner delivering his talk: Capturing Sunlight for a Sustainable Future taken by Michael Webb ©University of Cambridge
Recycling plastic waste is difficult and often unprofitable. Reisner group spinout Protonera has the perfect solution.
The Reisner lab has developed technology which can convert waste plastics with sunlight into hydrogen gas and valuable compounds such as glycolate, which is used in the cosmetics industry. Now the team has received initial funding to scale up this technology.
The process is based on collaborative research between the Departments of Chemistry and Biochemistry. It relies on enzymes which break down plastic waste, and synthetic catalysts that harness solar power to upcycle the solubilised plastics into high-value end products.
“Current recycling techniques often lose money,” explains Erwin, who co-founded Protonera and is Chief Scientific Officer. “They rely on getting high-quality plastics which need to be sorted and washed. By the end of the process the recycled plastic costs as much as virgin plastic that is produced from fossil fuels.”
Plastic-eating enzymes
In contrast, food-contaminated waste is ‘ideal’ for the Protonera technology. “We are not competing with other recyclers, because we can use plastics that currently cannot be recycled and so are being incinerated or put into landfill,” explains Erwin.
“The plastic-degrading enzymes work really well with contaminated plastics,” says Chief Executive Officer and co-founder Dr Jack Guo. “Not only can we use lower-grade materials, but we’re also able to produce high-quality, food-grade products.” Jack, who is an expert in enzymes, completed his PhD in the Department of Biochemistry with co-founder Biochemistry Professor Florian Hollfelder, who is the Scientific Adviser. The fourth co-founder is former Reisner PhD student, Dr Subhajit Bhattacharjee.
The technology can also be used to create low-carbon, high-purity hydrogen and compounds for use in the chemical industry. It works under ambient pressure and in normal temperatures, which is less expensive and more environmentally friendly than other methods. “We are not just making hydrogen but also mitigating waste,” explains Erwin. “We convert the CO2 into valuable compounds like glycolate, which at the same time prevents the production and release of damaging CO2 into the atmosphere.”
Challenges
“We need more efficient catalysts that harvest light better and produce more hydrogen from solar input. We want to improve each individual step and connect them all in a continuous process,” says Jack. “We will be working on the catalysts and the process.”
Working with industry
The team have been working with the Peterborough and Cambridge Waste Recycling partnership, who provide samples and feedback. “This is a huge opportunity for plastic recycling companies to transition to new technology. They are engaged
and interested. It’s a bit of a mismatch in scale, but they can see the potential,” says Erwin.
Five-year plan
The scale-up project has secured funding via the MATcelerate and TIF programmes administered by Cambridge Enterprise, which aims at transferring university-developed technology to market. Protonera has also received support from Founders at the University of Cambridge, an accelerator programme supported by Cambridge Enterprise.
“This funding will help us build our first bench-top reactor, that will be able to transform one kilo of plastic waste into high-purity hydrogen in one day,” says Jack.
“My ambition is translating research from our group into the real world,” explains Erwin. “Any contribution we can make to use sunlight to power the chemical industry is worthwhile.
If we can turn waste plastics into low-carbon, high purity hydrogen, we all win.”
This article was originally published in Chem@Cam magazine Issue 69.